Green technologies are driving the development of Tilos neoprene, revolutionizing the production process and its impact on the environment. With a growing focus on sustainability, researchers and manufacturers are exploring innovative approaches to create neoprene while minimizing its carbon footprint. These advancements include the adoption of renewable energy sources, the implementation of closed-loop recycling systems for neoprene waste, and the use of bio-based or recycled materials as substitutes for traditional petrochemicals. Embracing these green technologies not only promotes environmental conservation but also paves the way for a more sustainable and responsible future in the production of neoprene, benefitting both consumers and the planet alike.
LOVE OUR PLANET, THINK GREEN
A Better Neoprene
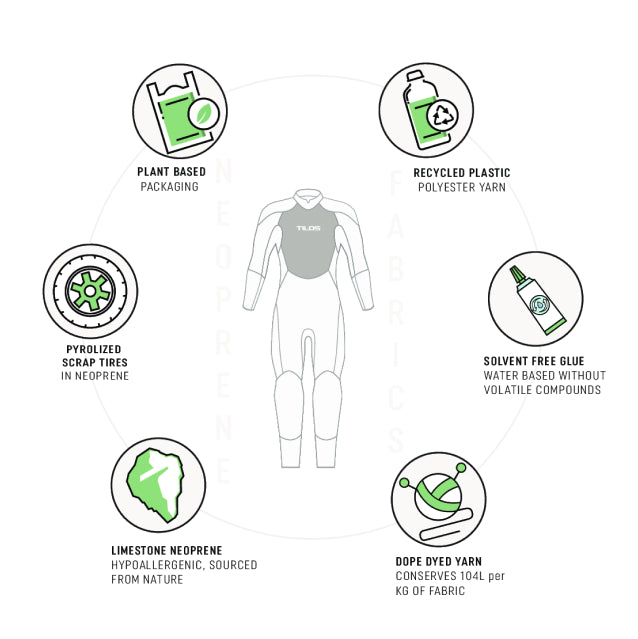
Neoprene RUBBER FOAM
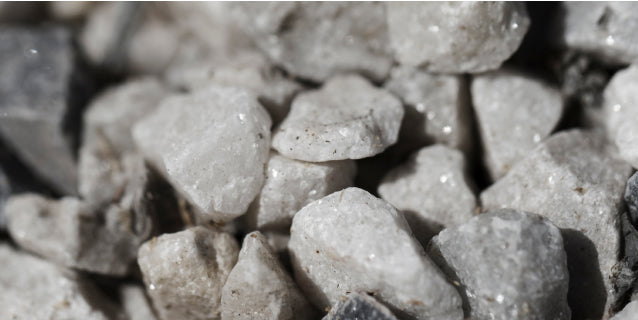
Limestone Neoprene
In the neoprene production process, limestone is utilized as a sustainable alternative to petrochemicals, resulting in the formation of rubber chips. This eco-conscious approach allows us to achieve comparable performance to conventional neoprene while significantly reducing our environmental footprint.
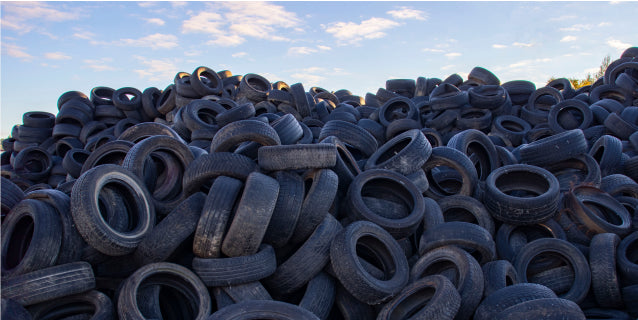
Eco Carbon Black
At our wetsuit factory, we prioritize sourcing a vital component of neoprene, Eco Carbon Black, from post-consumer scrap tires. This innovative practice substantially curtails energy consumption and lowers CO2 emissions by an impressive 200g per wetsuit, contributing to our commitment to environmental stewardship.
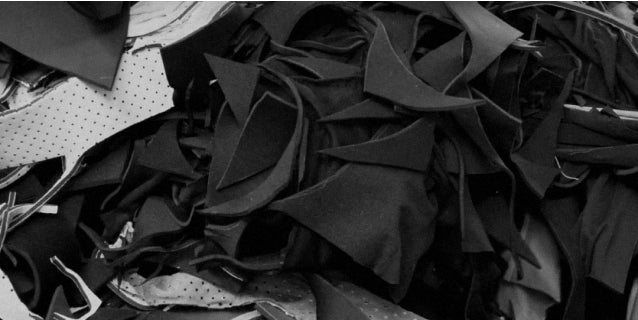
Neoprene Recycling Process
Following the neoprene creation process, the excess trimmed materials undergo a recycling and reutilization phase within the mixing process, leading to the production of additional neoprene sheets. This circular approach allows for substantial conservation of raw materials, a reduction in energy consumption, and a minimization of waste water and air emissions, all in line with our principles of resource efficiency and responsible manufacturing practices.
LAMINATION
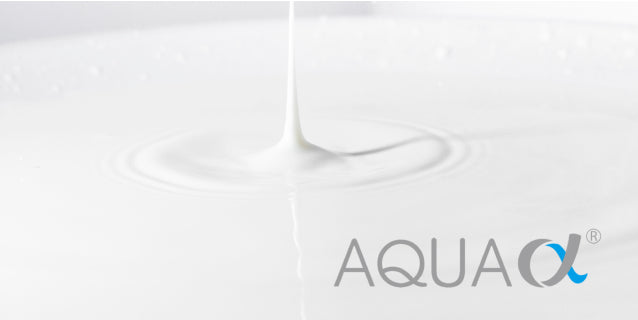
Water Based Glue
Water-based glues typically have lower volatile organic compound (VOC) emissions than solvent-based adhesives. This means they contribute less to air pollution and are better for the environment.
FAbrics
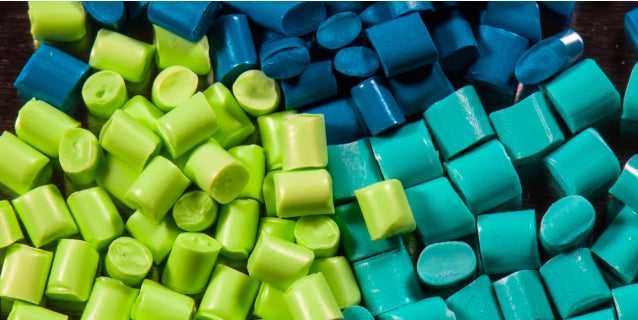
Dope-Dyed Yarn
We utilize the dope-dyeing technique for the yarn. This process involves infusing dye pigments into a molten plastic solution to create colored yarns. By adopting this method, we save significant amounts of water, reduce energy consumption, and minimize water pollution, reflecting our commitment to responsible practices.
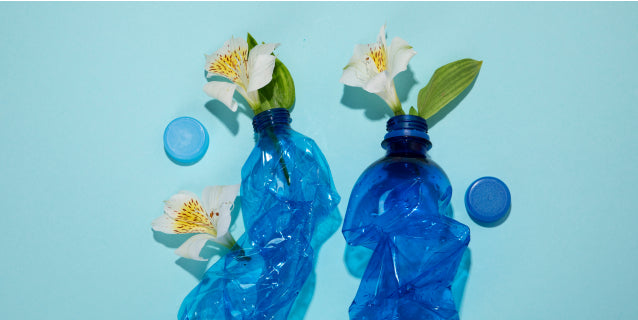
Recycled Polyester
A significant portion of our fabric collection is woven using polyester yarn derived from recycled plastic bottles. This approach not only aids in waste reduction but also optimizes material utilization.
GREEN TECHNOLOGITIES THAT CREATE MORE ECO-FRIENDLY NEOPRENE
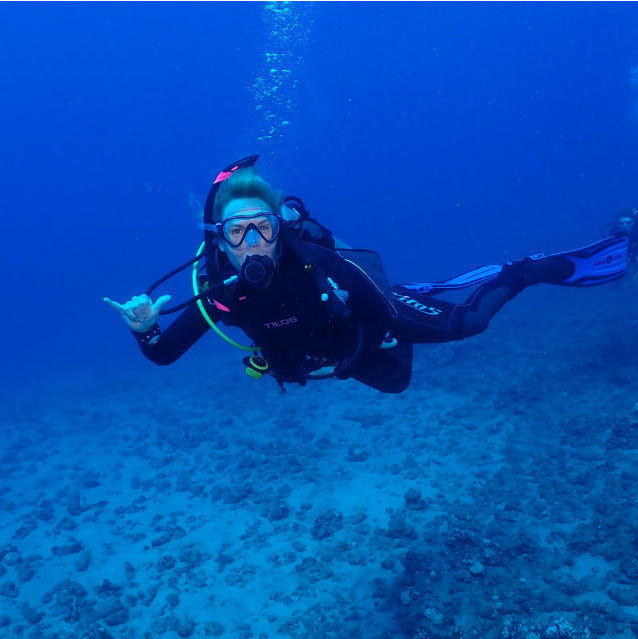
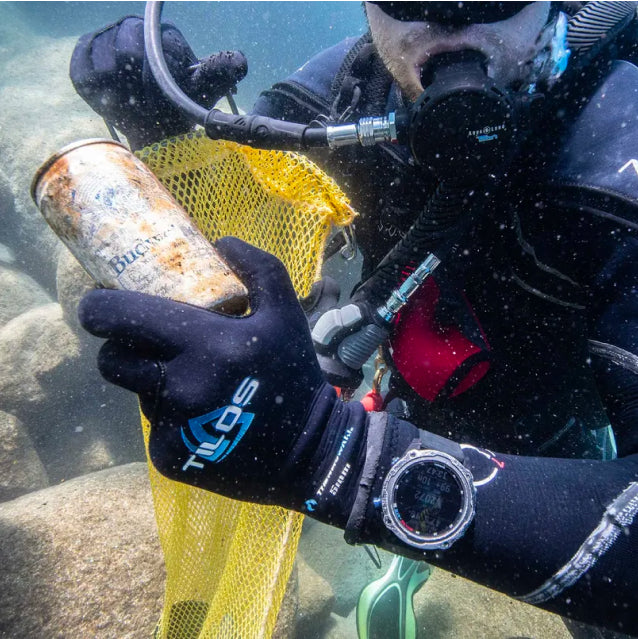